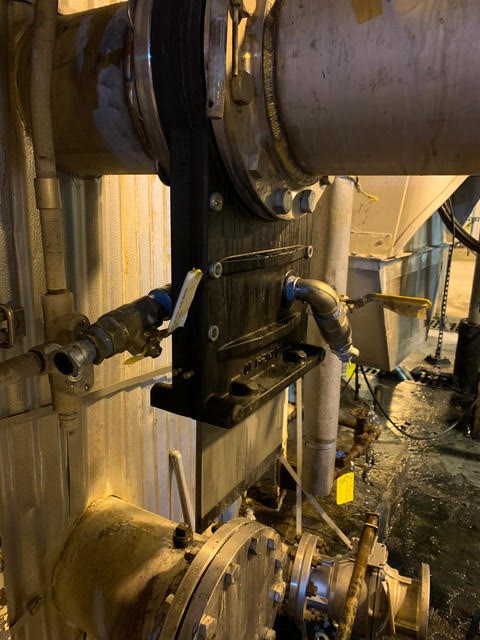
Green Liquor Application
Being able to Isolate various industrial processes is a critical part of the success and can have a big impact on the plant, and in this case study, the caustic area and chemical are at a container board mill.
The ability safely shut down a process line, whether it is for a planned maintenance during an outage , or an unexpected event posing a threat to employee safety or various equipment downstream of the valve requires the capability to close the valve at a moments notice. This case study will be a brief summary of multiple applications at key points throughout a mill in the caustic, lime kiln, powerhouse areas. All three of these areas can present some unique and challenging problems for Isolation Valve applications.
Most paper mills rely on ball valves in these locations because is an industry standard that is more expensive, but shutoff is reliable. If the process is dangerous or work is being done down stream of the valve, any amount of leakage is not acceptable. Ball valves are widely used on the dissolving tank outlet so that the process can be isolated upstream of the pump, instruments, other valves, etc.
The green liquor poses a huge challenge and sometimes in a very short period of time. The liquor can buildup in the ball valve cavity causing the valve to seize and when this happens, the valve is unable to do its job requiring replacement.
Wey Valve has a solution for these locations!
Traditionally, a large full bore ball valve has been the of choice in the locations. However, these installations quickly seize up and the operators can not open or close the valve without some type of assistance, come-a-long, or taking the valve our of service and cleaning the ball valve cavity. Wey can provide a Sheargate option that will solve all the inherent problems associated with the green liquor applications. Most of these installations will call for an 8” or 10” valve with the automated cylinder package with limit switches and solenoid. It is imperative to properly size the cylinder to overcome any buildup in the valve cavity that could occur over time. As the installation photo will show, we have the ability to provide a flush port on both the bottom inlet and outlet side of valve. This flush water can be controlled with a solenoid valve or simply manage flushing with manual valves. The customer can routinely maintain the valve by flushing after the valve strokes. During operation, the liquor will collect in the bottom cavity and if not flushed will build up and solidify. The water flush is critical to long-term operation of the valve.
The Wey Sheargate is supplied with multiple body materials, 316SS or Cast Ni-Resist Body. Its important to understand the seating arrangement and this give the Sheargate the ability to provide a zero bi-directional shutoff capability. The 440 seat rings are on both sides of the o-ported gate. When the Sheargate is in the open position, the valve acts as a continuation of the pipe, because the tolerances on the metal seat ring to gate and body are so tight, the Sheargate has no cavities for buildup. When the valve is in the open position, the port allow for flow then, upon stoke the port of the gate moves into the bottom of the valve body. Wey provides the transverse gate seal on both upper and lower body locations,. As with all Wey Valve designs, this is a two piece body. Because of this it is critical to the smooth operation that the customer pays attention to the installation and using the proper bolt lengths and bolt torque when installing.
Again, after the valve is fully stroked, flushing will greatly enhance the overall performance of the valve allowing for longterm operation. The Wey Sheargate can be the best solution to these most difficult applications in your mill.
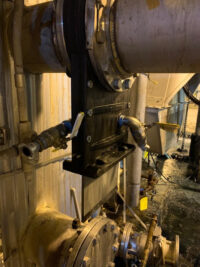
Containerboard Mill
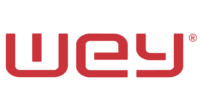
Wey Valve Solutions
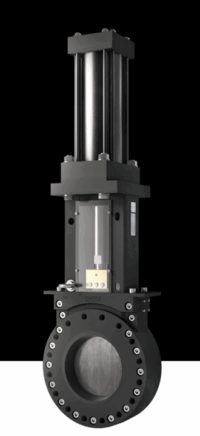